Sponsored by
The more complex the environment, the more that can go wrong. This has been borne out for decades in enterprise sectors that run high-cost, but high-return operations. Automotive is a perfect example of this—end-to-end challenges raise the stakes for companies, and solutions that can minimize the impact of disruption are immensely valuable. Automotive players face extreme downtime costs, significant product development costs, and rapidly shifting consumer sentiment. The supply chain for automotive is equally complicated, with tiers of global suppliers each integral to an OEM's operation.
With complicated supply chains spanning the globe, automotive operators are beholden to every facet of their value chain to maintain production. If a parts supplier experiences unexpected downtime, the impact is felt through the rest of the value chain up to the OEM.
In the quest to keep downtime to a minimum and streamline operations through the entire value chain, AR can do both. Reduced error rates and increased safety for workers are matched with reduced operational downtime, reduced travel time and costs, and, ultimately, increased operational efficiency. Companies have some choice on how to implement AR with variables like upfront cost, level of desired integration, target use cases, likely users and usage environments, and safety needs all dictating what approach is best.
Download the whitepaper to learn more.
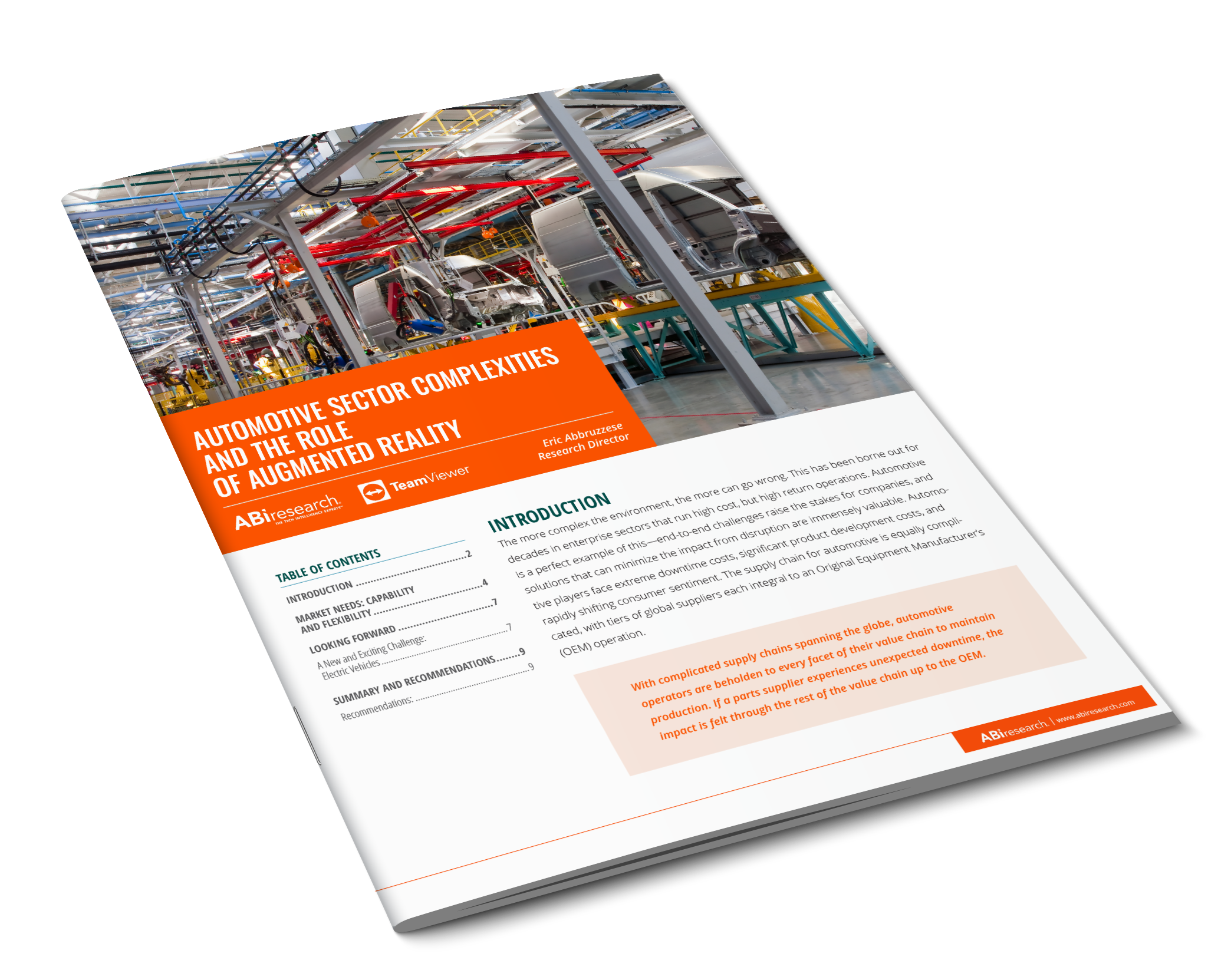